INNO-20182009
The project aims to establish an optimal, efficient and lightweight design methodology in the manufacture of medium-large components, taking full advantage of the capabilities of FADDE technologies
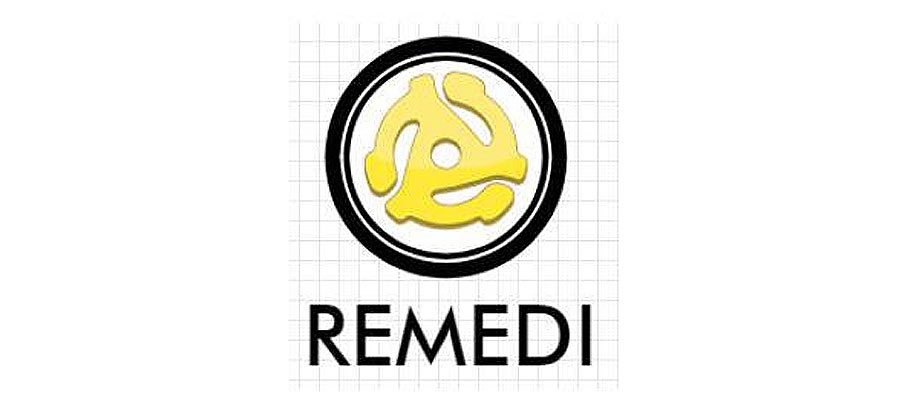
Smarmec, a company specialising in the design, industrialisation and manufacturing of mechanical, electrical and electronic engineering solutions, is part of the international REMEDI consortium, in which it will collaborate through its Zamudio production facilities.
The main objective of the REMEDI project is to establish an optimal, efficient and lightweight design methodology in the manufacture of medium-large components, taking full advantage of the capabilities of FADDE technologies (Direct Deposition Additive Manufacturing) using laser technology and addition of metallic powder.
In this way, REMEDI aims to overcome some of the current barriers related to aspects of design optimisation and productivity in the digital manufacturing of medium-large components with high added value, manufactured using laser metal deposition technologies, which prevent greater acceptance of this technology in the sector. Thus, these processes involve a value chain consisting of the design, process configuration, process planning, manufacturing with online control/monitoring, post-processing, and quality control phases. Out of all of these, for a type of manufacturing technology based on the possibility of generating shapes with a greater degree of freedom, it is the redesign phase that really offers greater added value and the most relevant benefits. Therefore, REMEDI will focus on using these different stages of manufacturing to provide feedback to the design itself, up to its most efficient optimisation.
Based on this industrial need for this emerging technology, REMEDI’s goal is precisely to establish the design methodology for Laser Metal Deposition (LMD) processes with the intention of reducing the significant consequences of the design in the final quality of the piece.
To implement the concept of Quality-by-Design (QBD) in the manufacturing of the project prototypes, a software/hardware platform will be used that will consist of:
- An offline engineering unit, which integrates different commercial CAx technologies under the same layer.
- A physical additive manufacturing installation via LMD, to implement a Quality by Design methodology and validate it for the additive manufacturing of large components optimised to achieve zero defects.
Specifically, this environment will be implemented at two manufacturing facilities (a Spanish factory, Smarmec and a Turkish factory, Coskunoz R&D), to demonstrate the concept and obtain the future reproducibility capacity in any demanding industry. The REMEDI technology will be validated for two different sectors demanding high added value components: space applications and aircraft components.
The proposed objectives will be achieved by following these technological milestones:
Performing a topological optimisation of the design of the piece based on the structural integrity requirements and functional loads, to provide a more efficient component in terms of raw material use, production cost and delivery time.
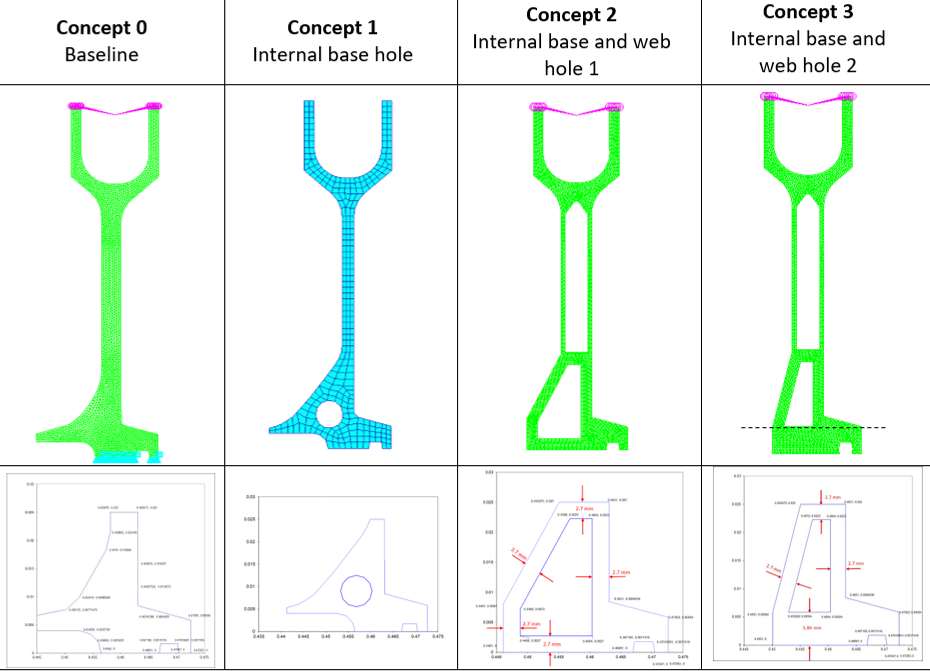
Determining the manufacturability capacities of the LMD process in its different configurations of system parameters/process parameters, in order to feed the Topological Optimisation tool with data from real industrial scenarios.
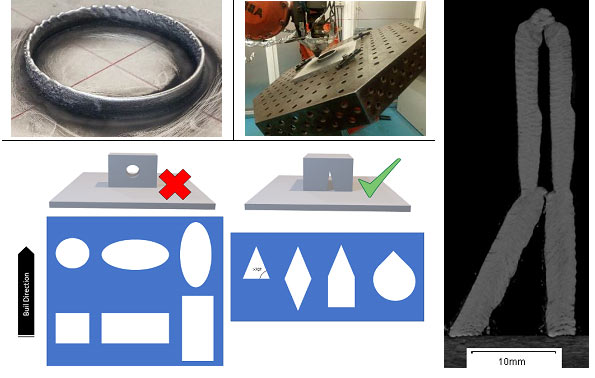
Acting on the cycle system configuration/deposition strategies/multiphysical simulation to reach a thermal equilibrium, which at the same time serves to automatically evaluate the design of the piece obtained in the previous steps, detecting areas of the piece that may be conflicting for its manufacture or for the final functionality of the piece.
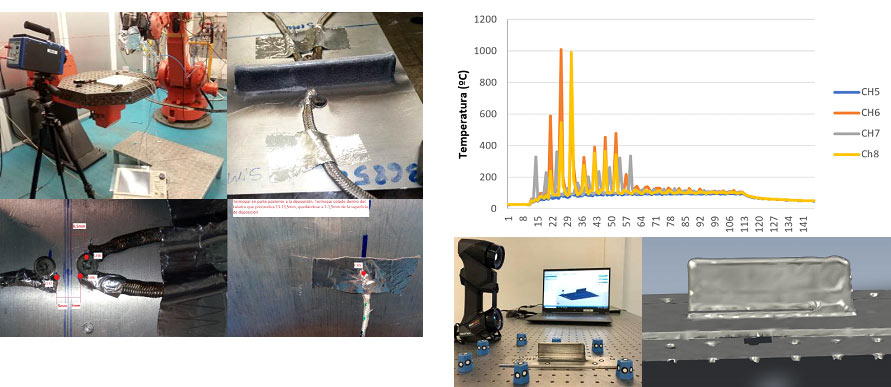
Analyse the data linked to the laser power and the temperature of the molten bath at any point in the process by means of monitoring systems, to link them to the design stage and propose new design changes based on this.

Remedi Consortium
To undertake this ambitious challenge, a national multidisciplinary consortium composed of 3 companies has been set up, with the necessary skills and knowledge to cover the project’s entire value chain:
- CT INGENIEROS, provides engineering services for a wide range of activities from the product design stages to engineering activities and maintenance processes in different sectors: aeronautics, rail, automotive, naval, renewable energy and industrial plants (Product design, Manufacturing Engineering, Design and Calculation Tools or Quality Engineering, among other aspects).
- RAMEM, as an SME dedicated to the design, manufacture and assembly of mechanical and electromechanical equipment, mainly for the aeronautical and aerospace industry. For these applications, it offers services that cover the entire value chain, from the design phase, manufacturing engineering or the development of tests and quality control.
- SMARMEC, spin-off of the company Tecnichapa, offering complete solutions to its customers in the sector of fine and precision sheet metal work. In REMEDI’s area, its experience in the development of solutions and manufacturing for prototypes and small series of components with high added value is of vital importance.The consortium has the support of AIMEN Centro Tecnológico, an entity with extensive experience in the development of laser technologies, in the development and commissioning of additive manufacturing processes and in the development of monitoring and control solutions for these.
In addition, at European level the consortium is completed by the Turkish partners Coşkunöz R&D and TAI (Turkish Aerospace Industries).
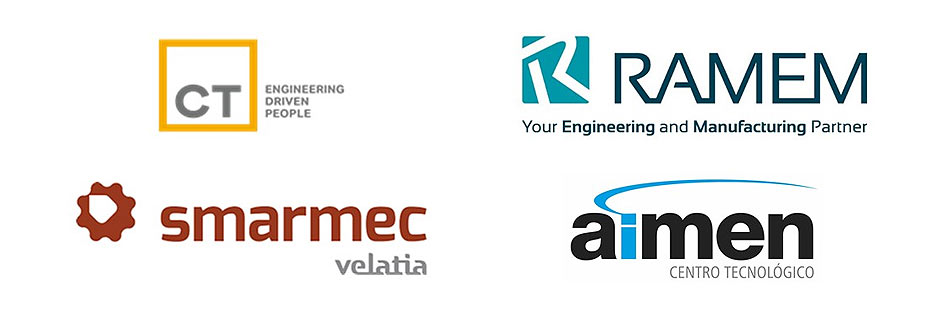
Budget and financing
The REMEDI project will last 30 months (it is expected to end in 2021) and has an approximate budget of €2M. The international project has been approved under the SMART EUREKA Advanced Manufacturing call. At national level, the project is subsidised by the CDTI through the INNOGLOBAL 2018 programme, and supported by the Ministry of Science, Innovation and Universities with a total budget of €1,335,516.00, and a total grant of €392,657.00.
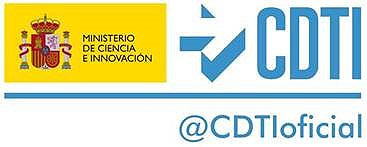
A Project funded under the SMART EUREKA CLUSTER on Advanced Manufacturing programme.
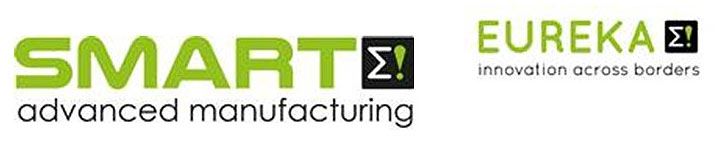