Industrial boilermaking, with a tradition going back centuries, is still just as important to our society in the 21st century
As we mentioned not so long ago in our post explaining industrial welding, our society is made of metal; a material as mundane as it is marvellous. That is why today we want to shed some light on a process with little glamour but with a lot of technological knowledge: industrial boilermaking. A process that has its roots in the Middle Ages, when it emerged as a craft trade dedicated to the manufacture of boilers (hence its name), metal containers and other metal objects for various uses, including the transport of liquids and foodstuffs, as well as construction and architecture.
Nowadays, industrial boilermaking is a branch of metallurgy dedicated to the manufacture and assembly of metal structures, or metal sub-assemblies of different types, for industry. Basically, it involves transforming simple metal parts into highly complex assemblies and structures that require precision, technology, skill and innovation in the handling of the materials, tools and machinery used during the process. This is why not all companies are able to carry out this task professionally and efficiently.
These highly complex and precise metal assemblies or sub-assemblies are prepared to end up forming part of machinery, ships, large storage tanks, pipes and structures of all kinds. This makes industrial boilermaking a highly specialised branch within the manufacture of metal structures, regardless of the sector.
What materials and processes are involved in boilermaking?
In industrial boilermaking, materials such as steel, iron and aluminium, among others, are used, depending on the sector for which they are intended and the requirements of the end product itself. This versatility of materials is, in turn, a challenge for each company, which must adapt its production and design methods according to the type of material to be used, thus optimising the manufacturing process.
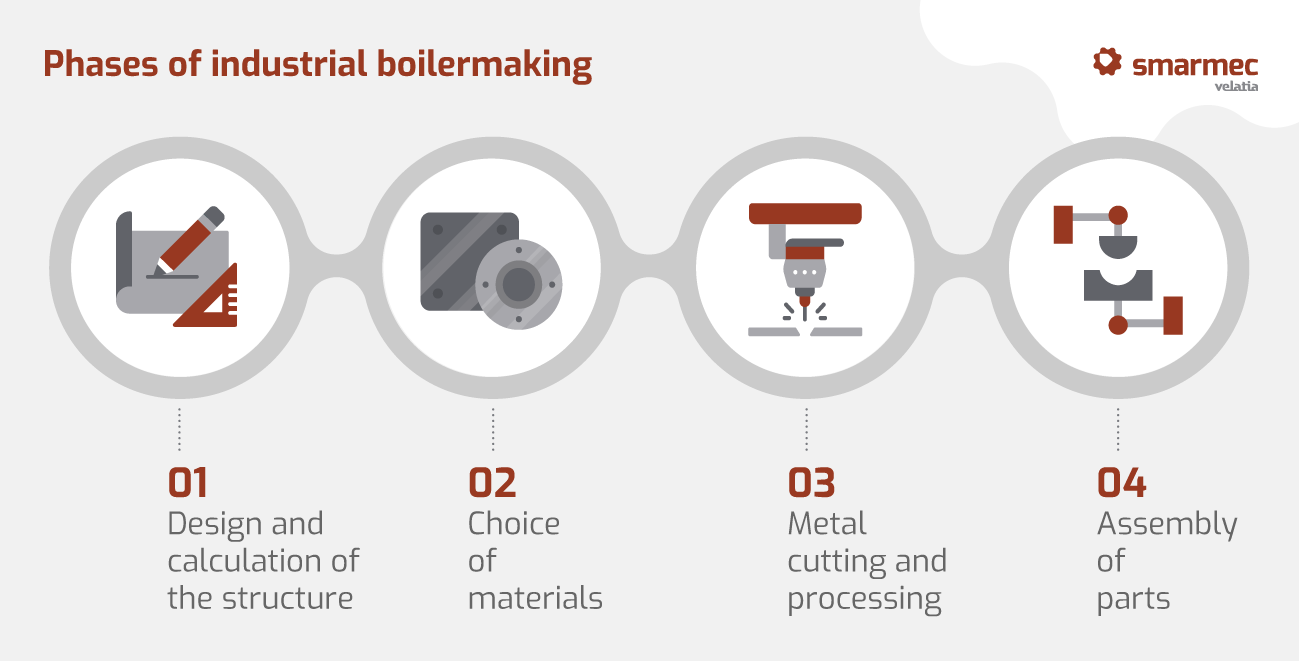
The industrial boilermaking process begins with the design and calculation of the metal structure, in which the measurements, materials and processes to be used are defined. Then, the metal is cut and shaped using techniques such as plasma cutting, laser cutting, punching, bending and forming, among others.
Once the parts have been cut and shaped, they are assembled, using techniques such as welding, riveting or screwing, depending on the needs of each project.
Industrial boilermaking requires highly trained professionals specialised in the use of specific tools and machinery, as well as in the reading of technical drawings and diagrams. In addition, it is important to have a team with extensive experience in the manufacture of metal structures, capable of guaranteeing their quality and durability.
Smarmec, more than 40 years of experience in boilermaking
As we have seen, industrial boilermaking is an activity that requires high levels of specialisation, technology and quality to meet the high standards demanded by the market. Something that we at Smarmec have more than internalised. The Smarmec brand was born in 2016 within Velatia, with the experience of more than 40 years of Tecnichapa, founded in 1982 with the aim of offering integrated solutions to its customers in the fine and precision boilermaking sector.
Thus, we respond to metal-mechanical based products, where we integrate technologies supported by a wide network of partners and local suppliers in each of our locations; both in Europe and Asia.
Do you want to know more?